The start of each process is the project received from the customer: it can be in different formats - manual drawing, pdf - and is able to maintain a high technical profile of the project.
Then comes the design phase, where specialized engineers study and analyze which options to make the most of during construction.
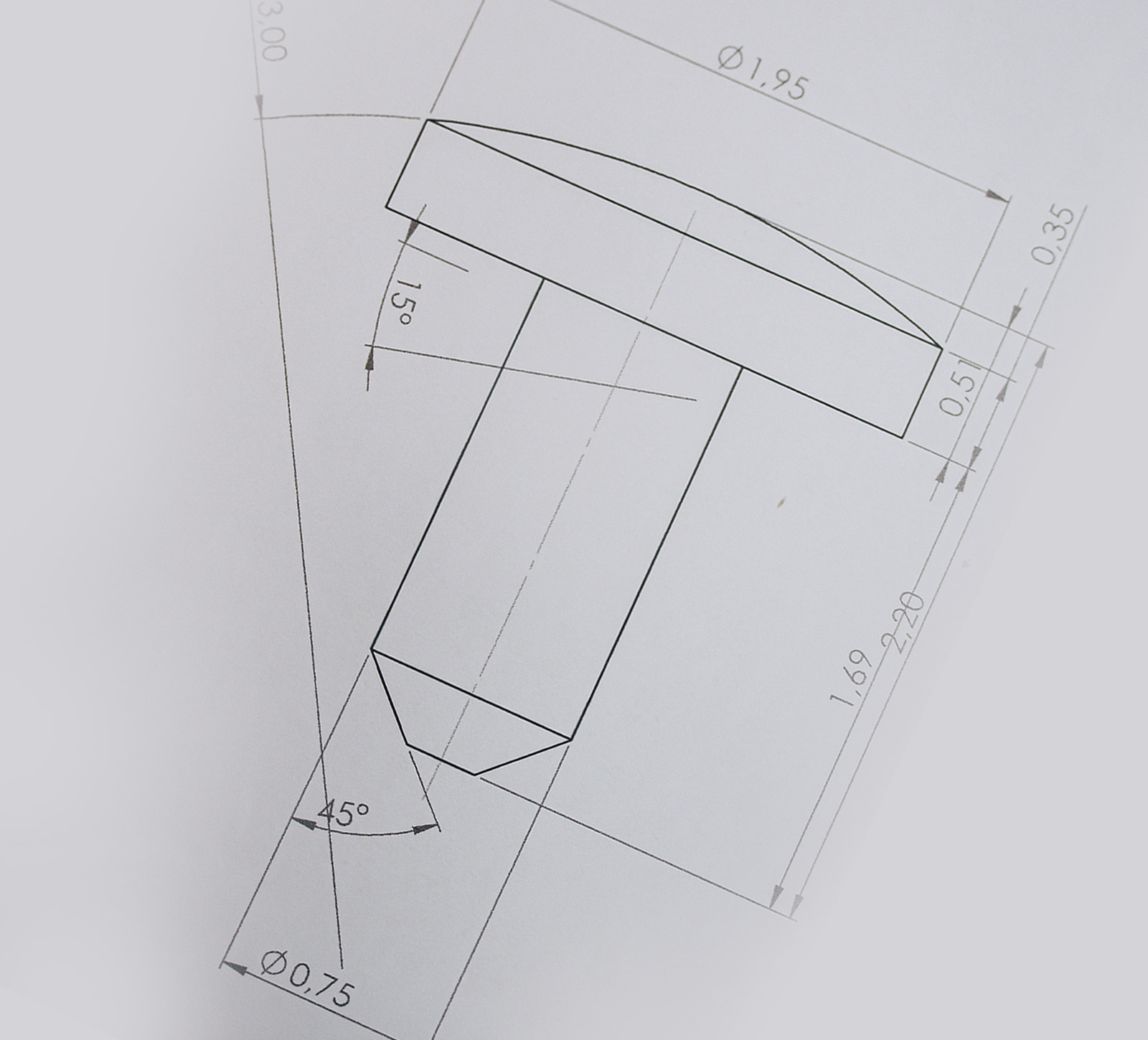

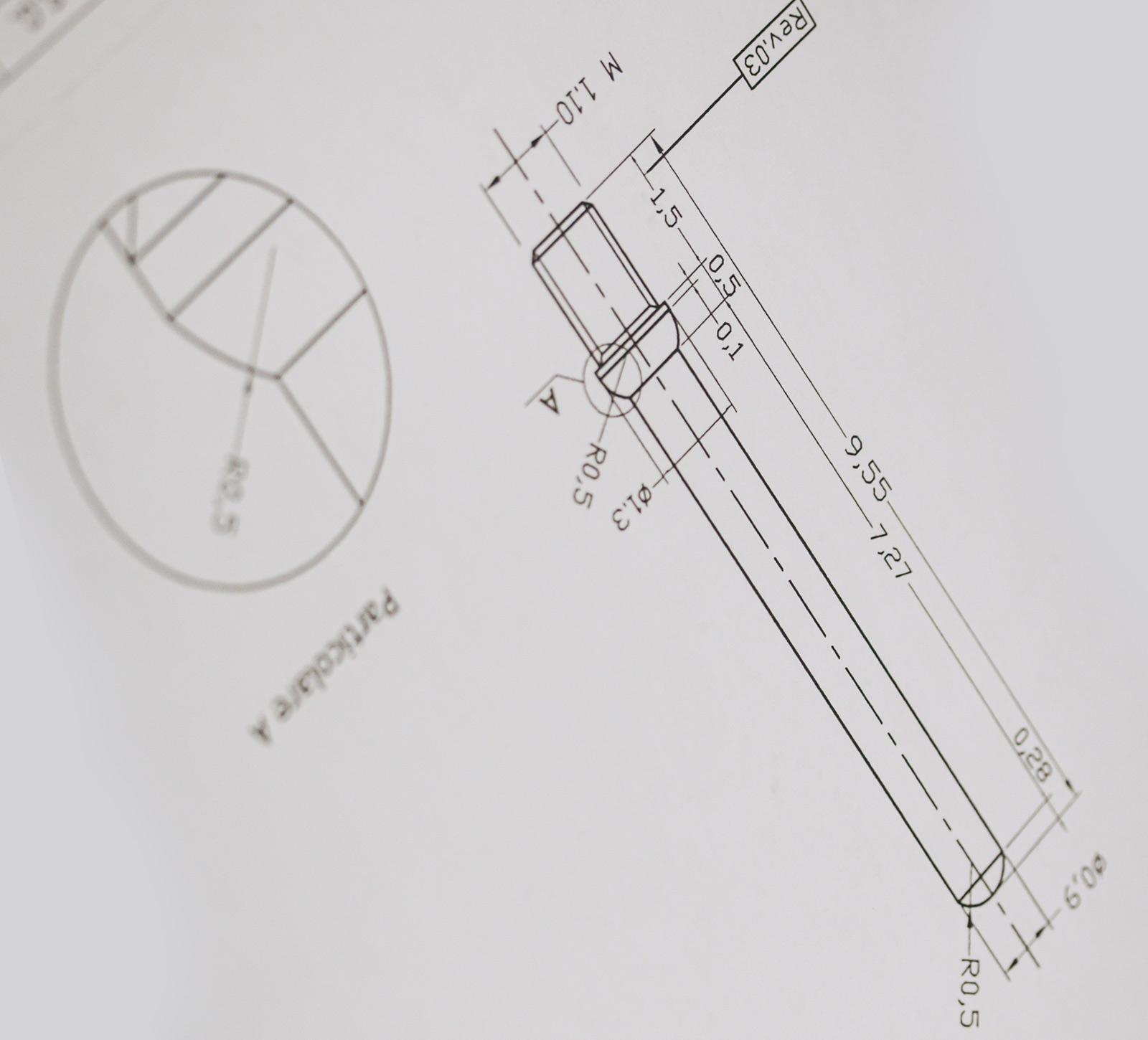
Through the high-tech machinery, the precision in the production of the various pieces has a perfect and optimal technical yield. Where tradition does not reach, machines arrive, which through the dimensions, measurements and specific information, allow the creation of a prototype of an object without imperfections.
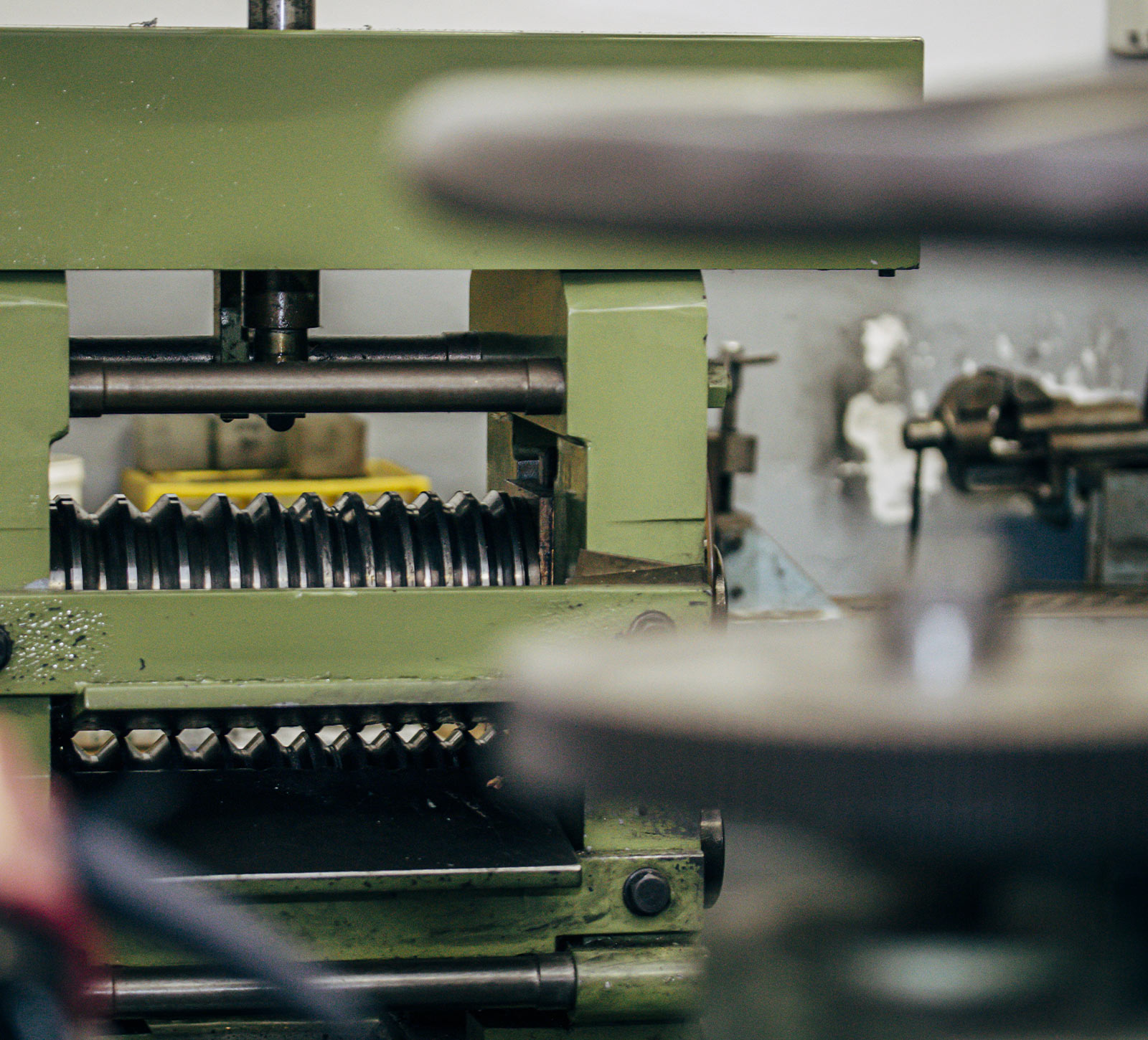
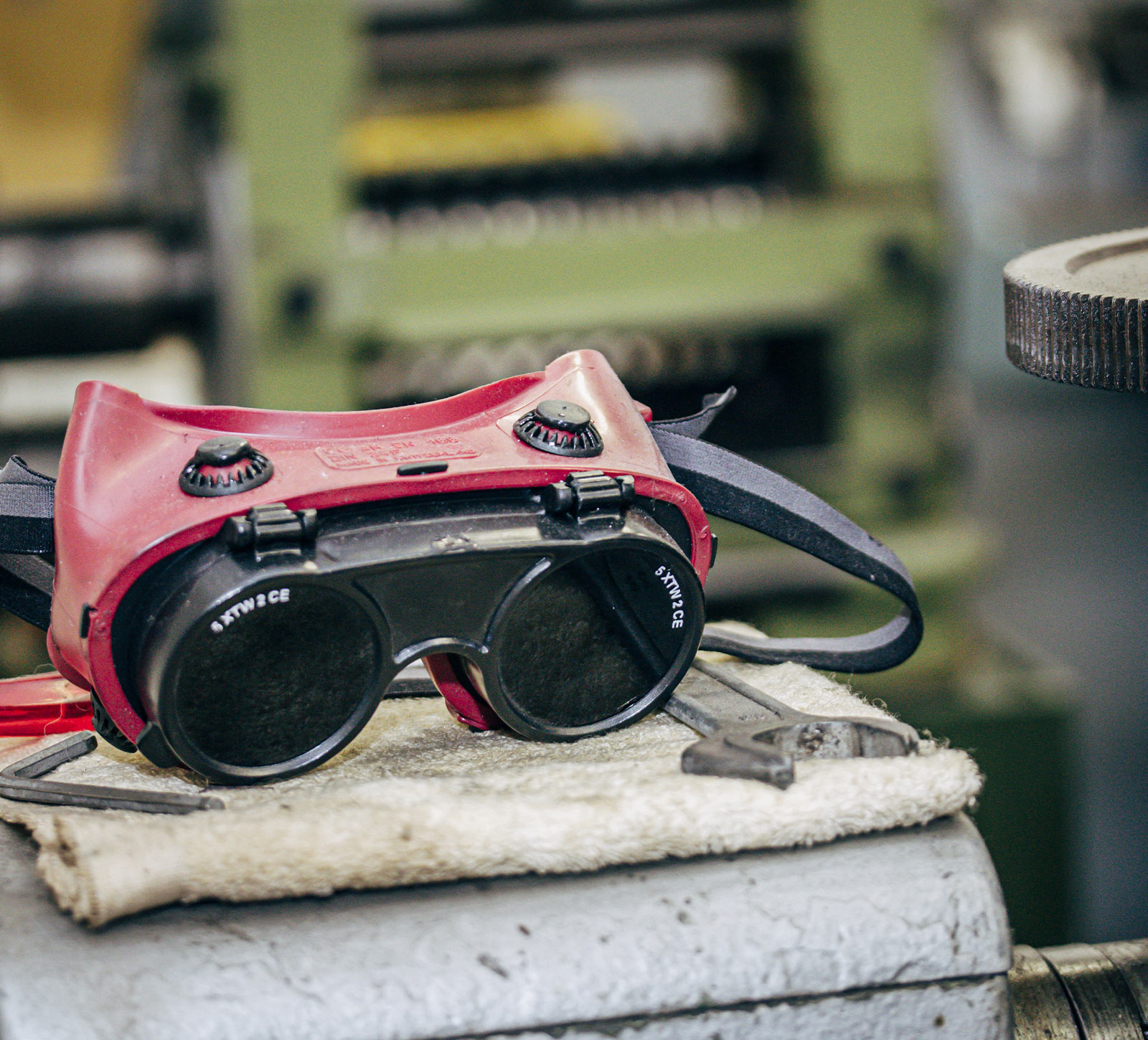
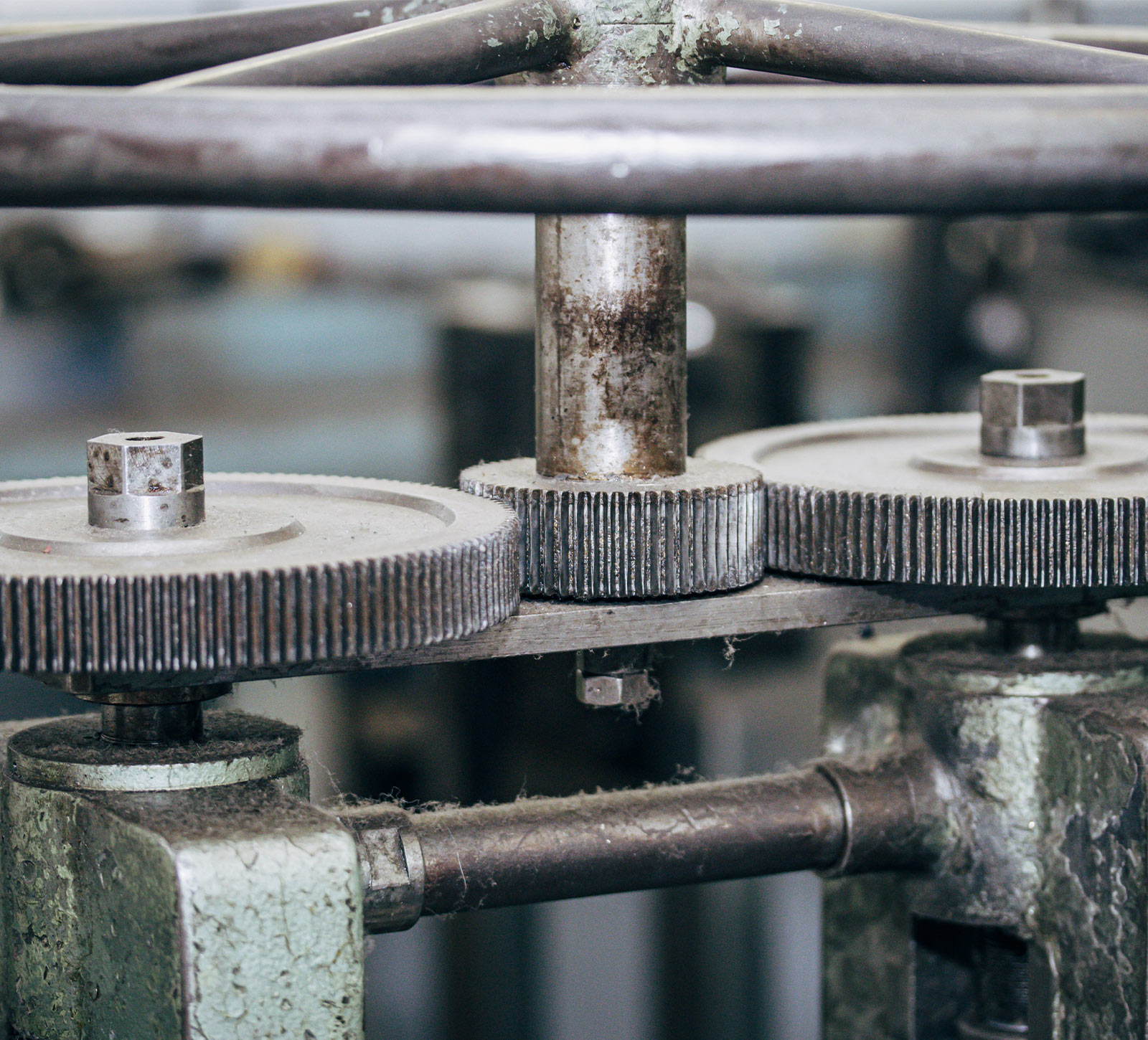
Casting is the first operation of all stages of production, in which Gold and fine Silver are used.
All karats of Gold, 9, 14, 18 and all alloys are included, according to each customer and his personal preference.
The lamination process is the next step and consists in the reduction of the wire into various shapes: round, square or hexagonal. The wire is heated, so that it is easily malleable and adaptable to the desired shape. It is then immersed in a tank of water to harden and finally it gets dried. Then is moved on to the drawing of the material that through the use of cylinders of various sizes, allow the object to reach the desired dimension.
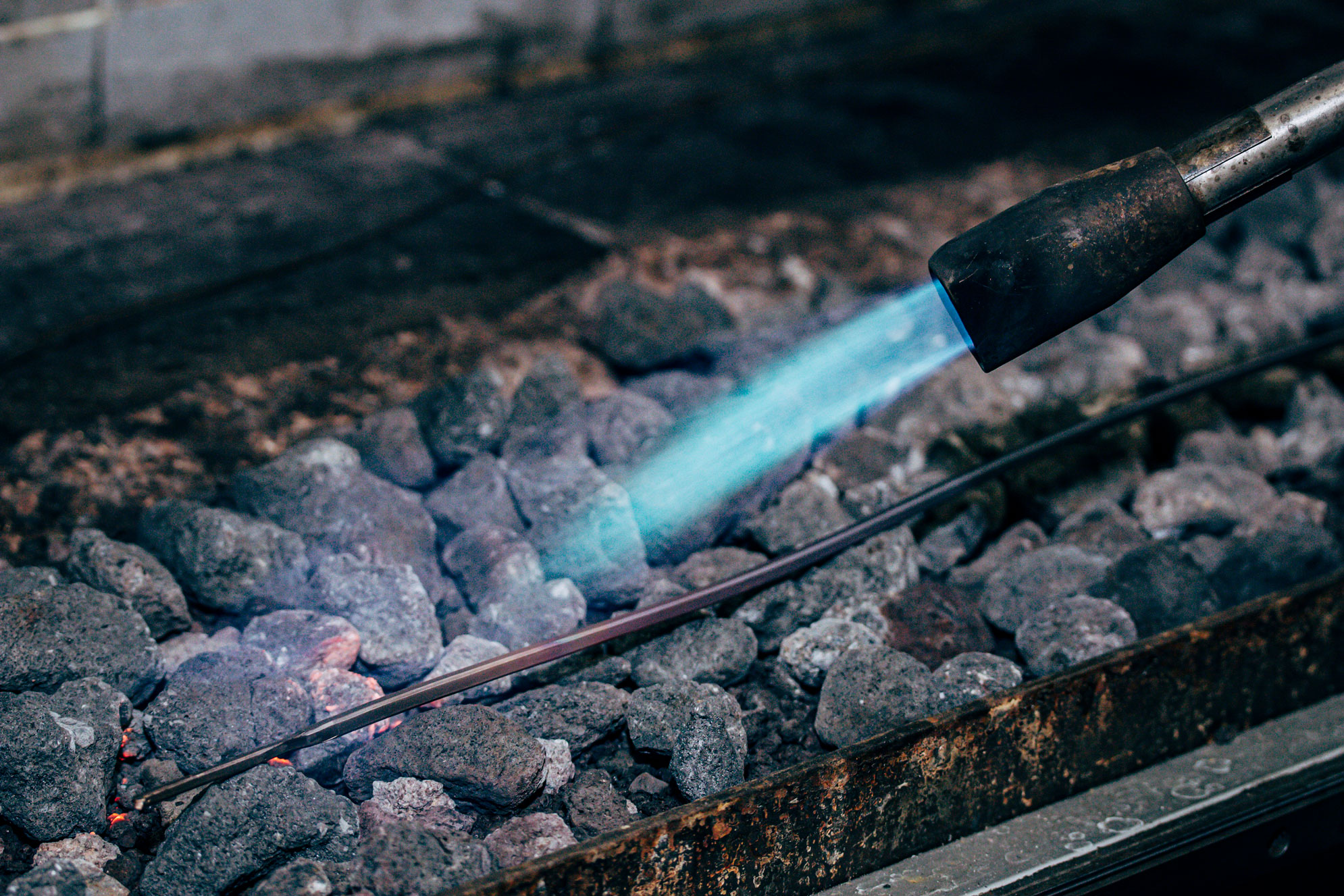
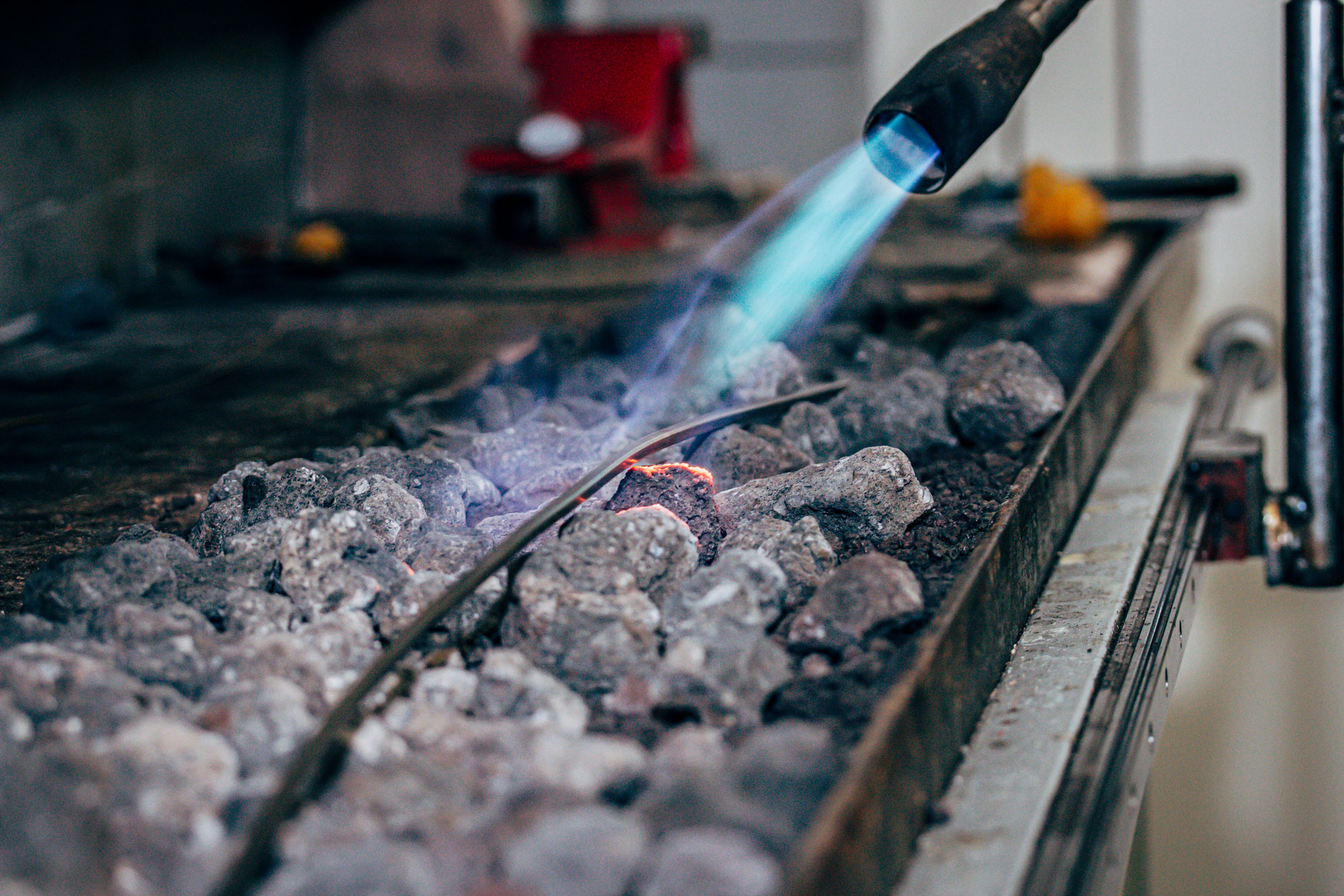
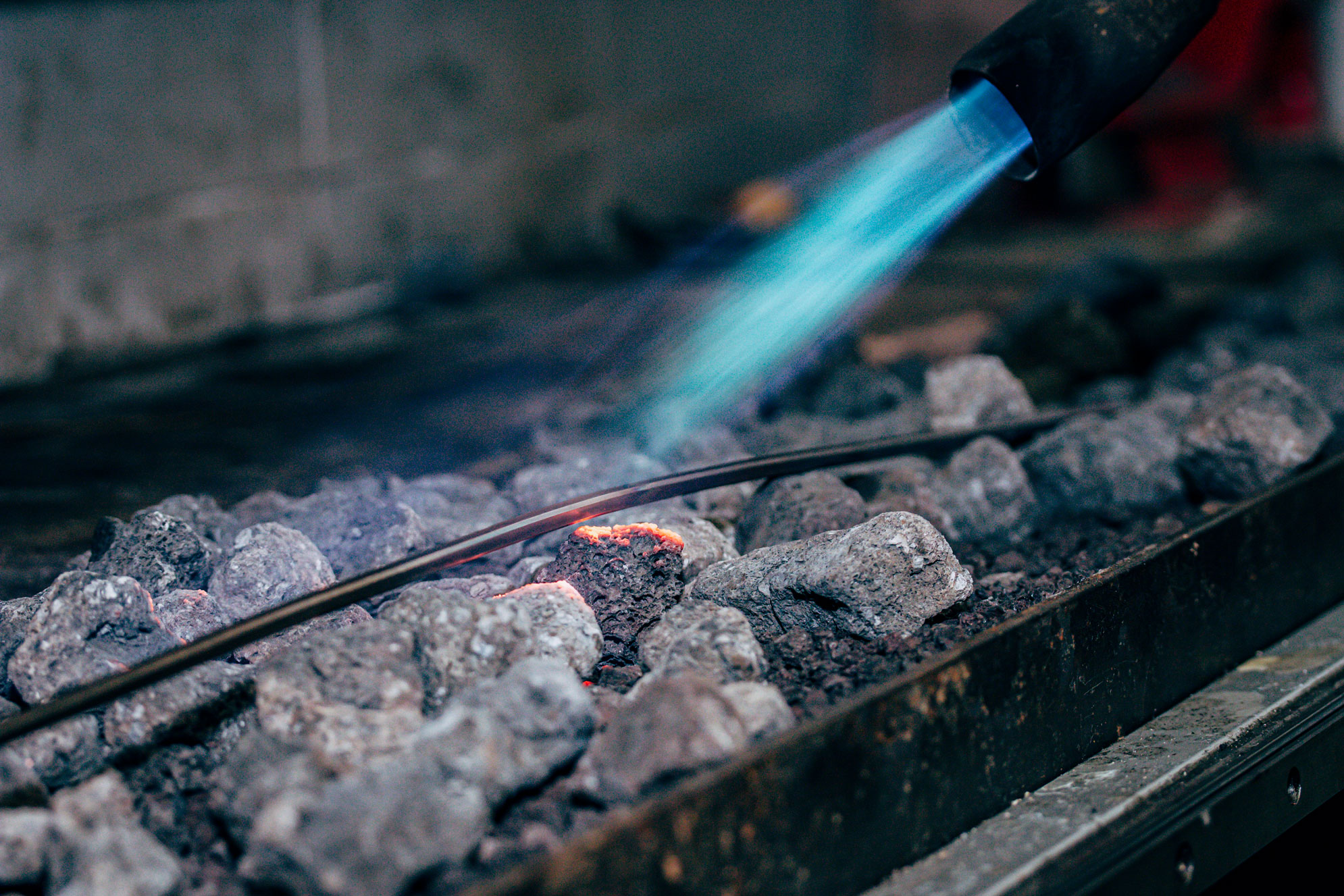
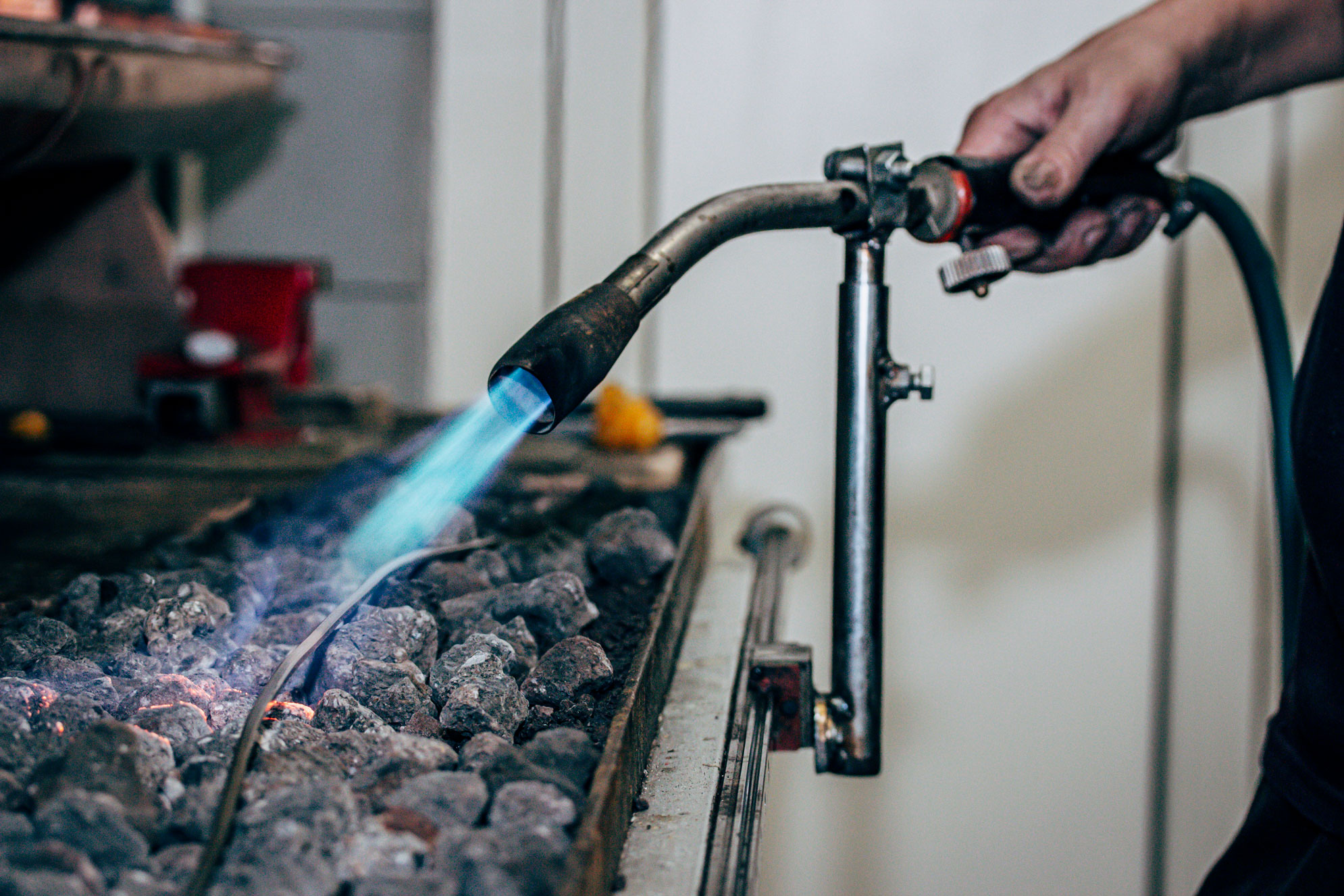
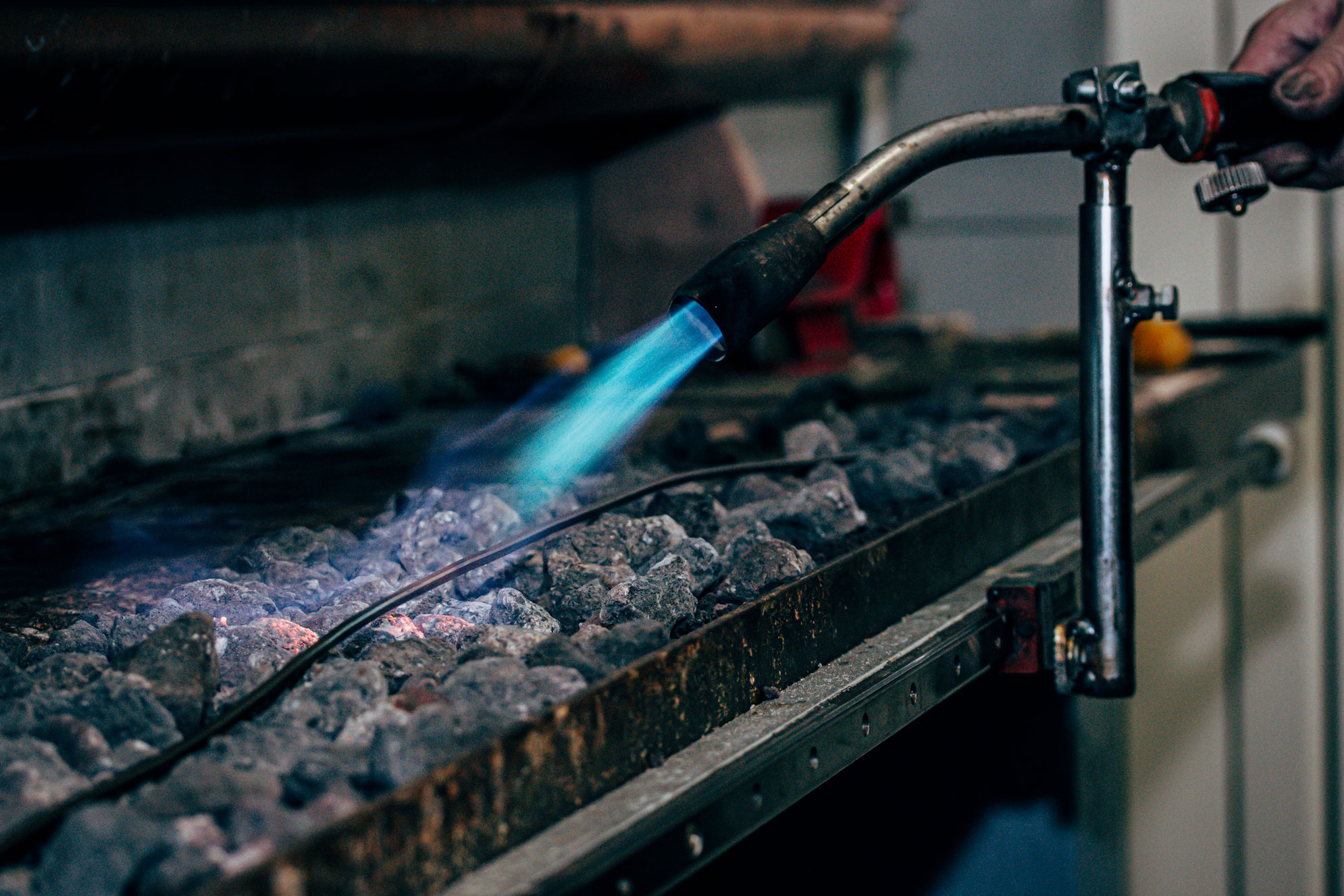
These three phases define the final shape of the semi-finished product, through the use of the latest generation machinery: turning, through lathes of different sizes, it gives to the material the desired form.
With the threading, the details and finishes of the object are defined. Finally comes the parting step, where the useful part of the object is cut creating the final semi-finished item.
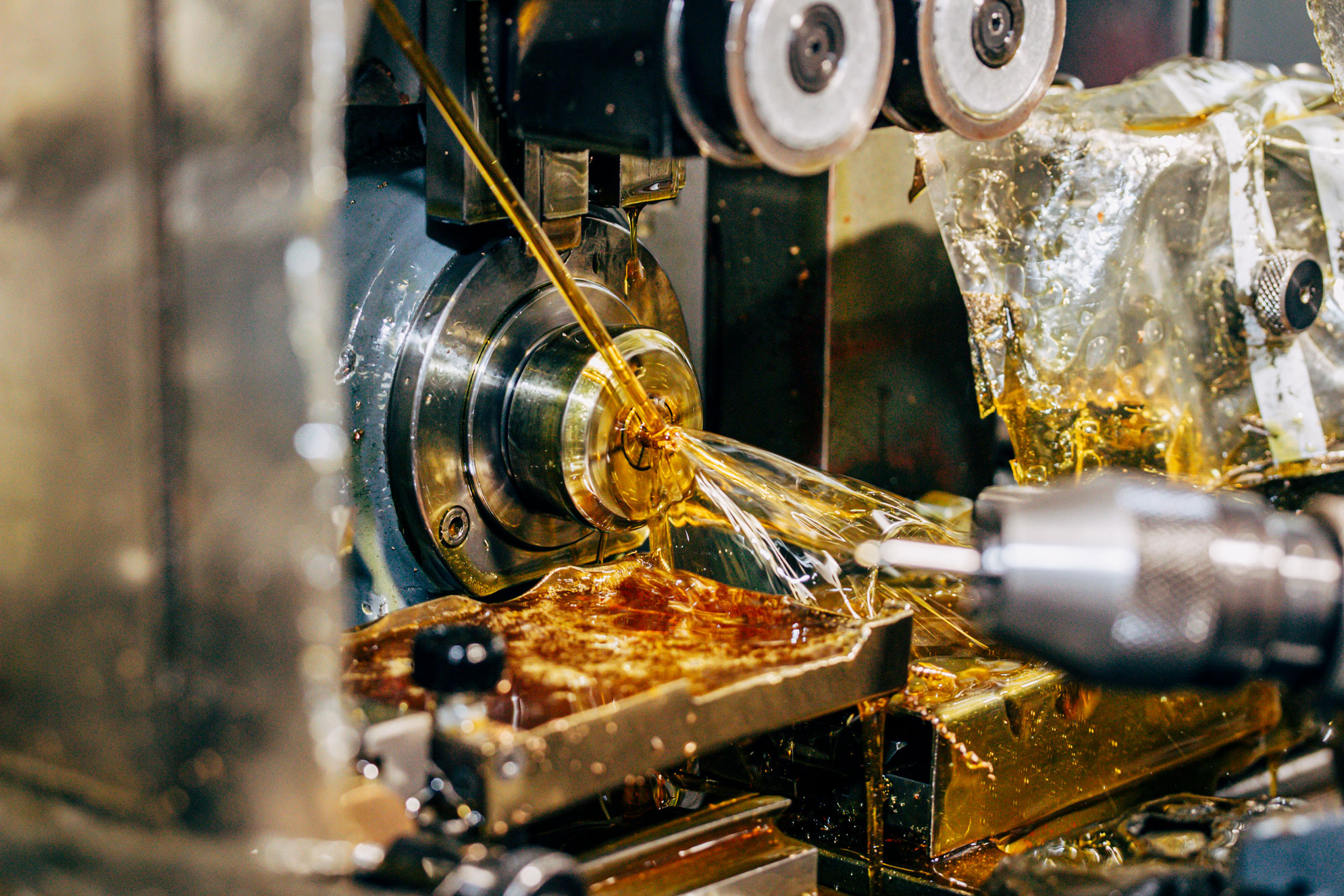
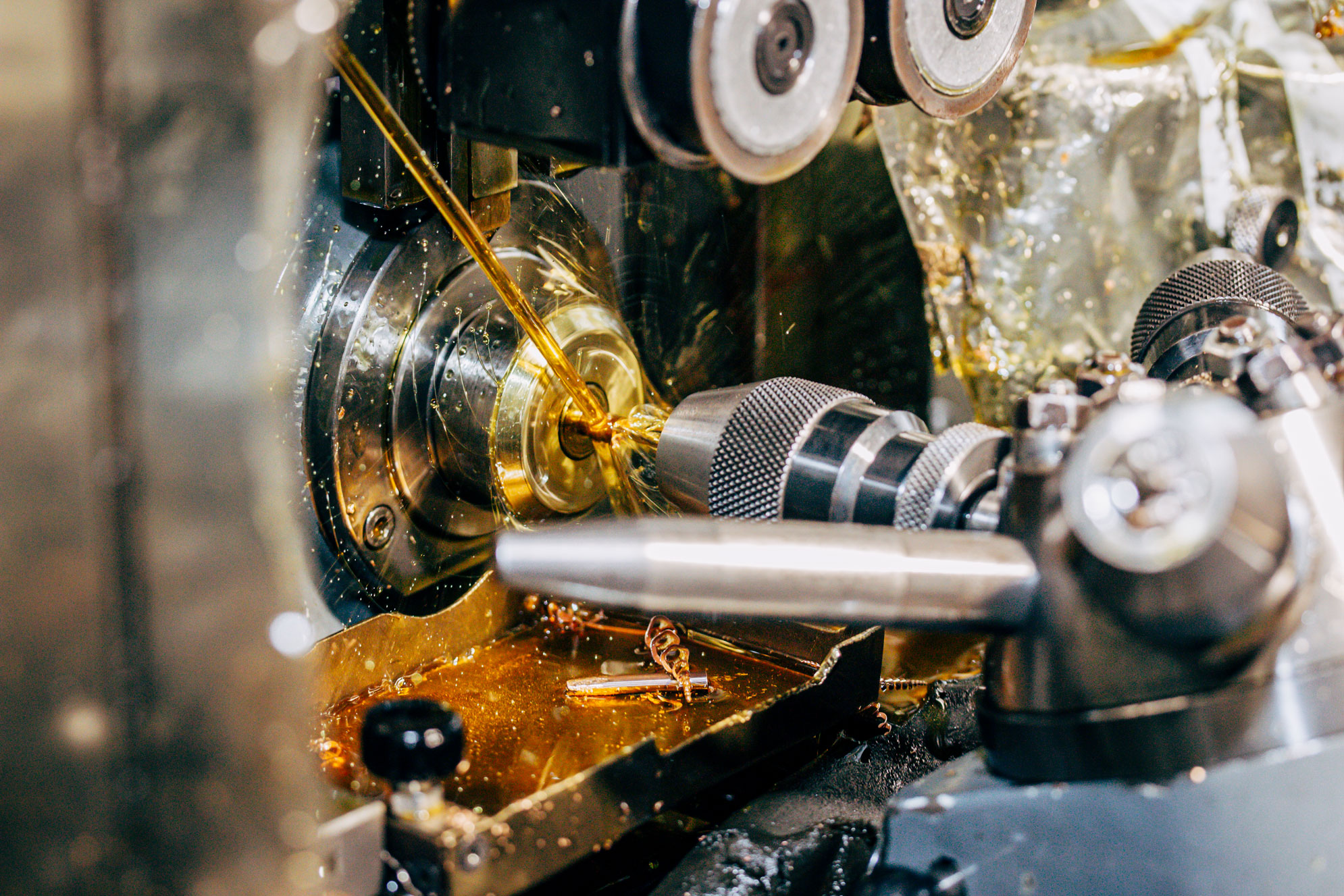
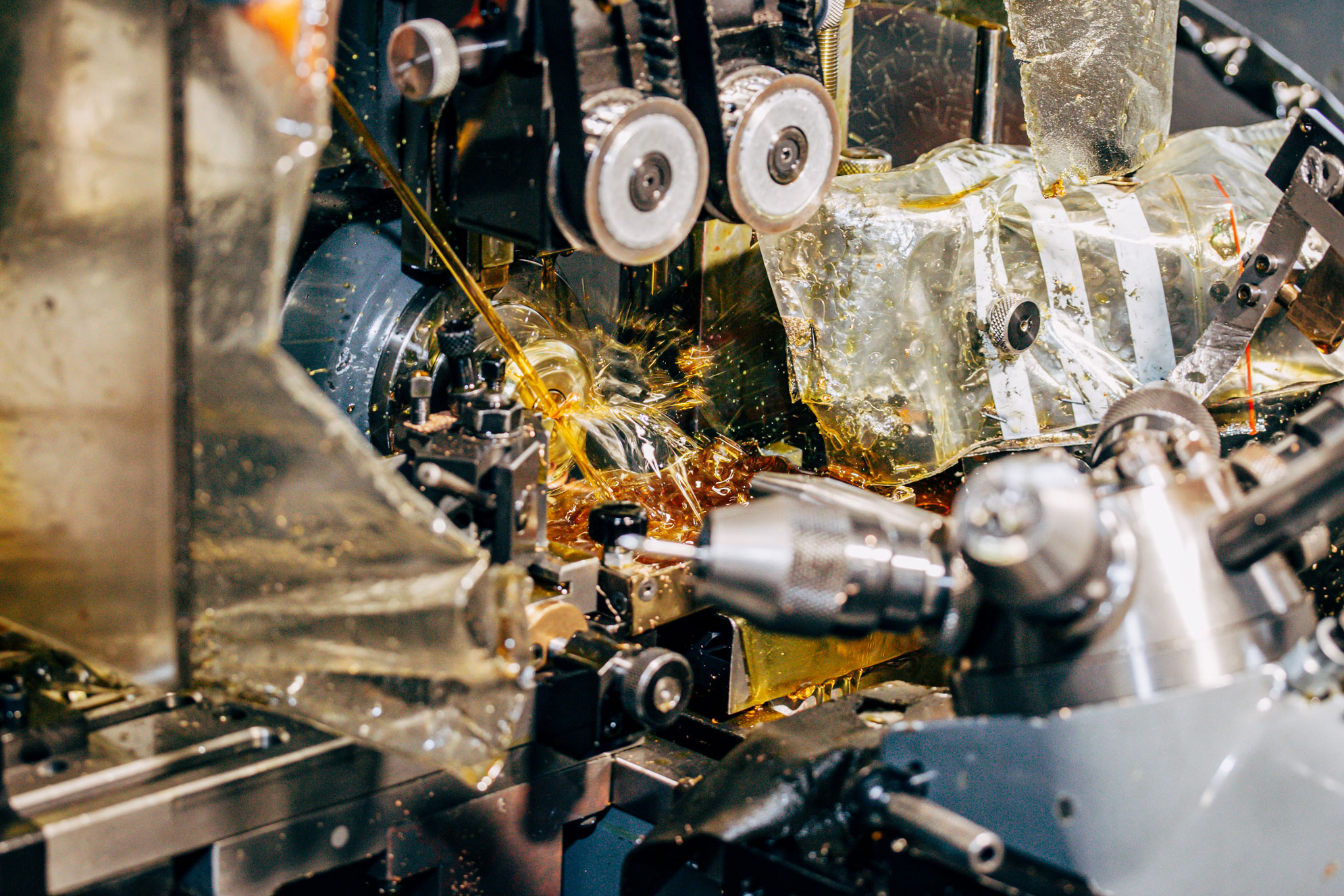
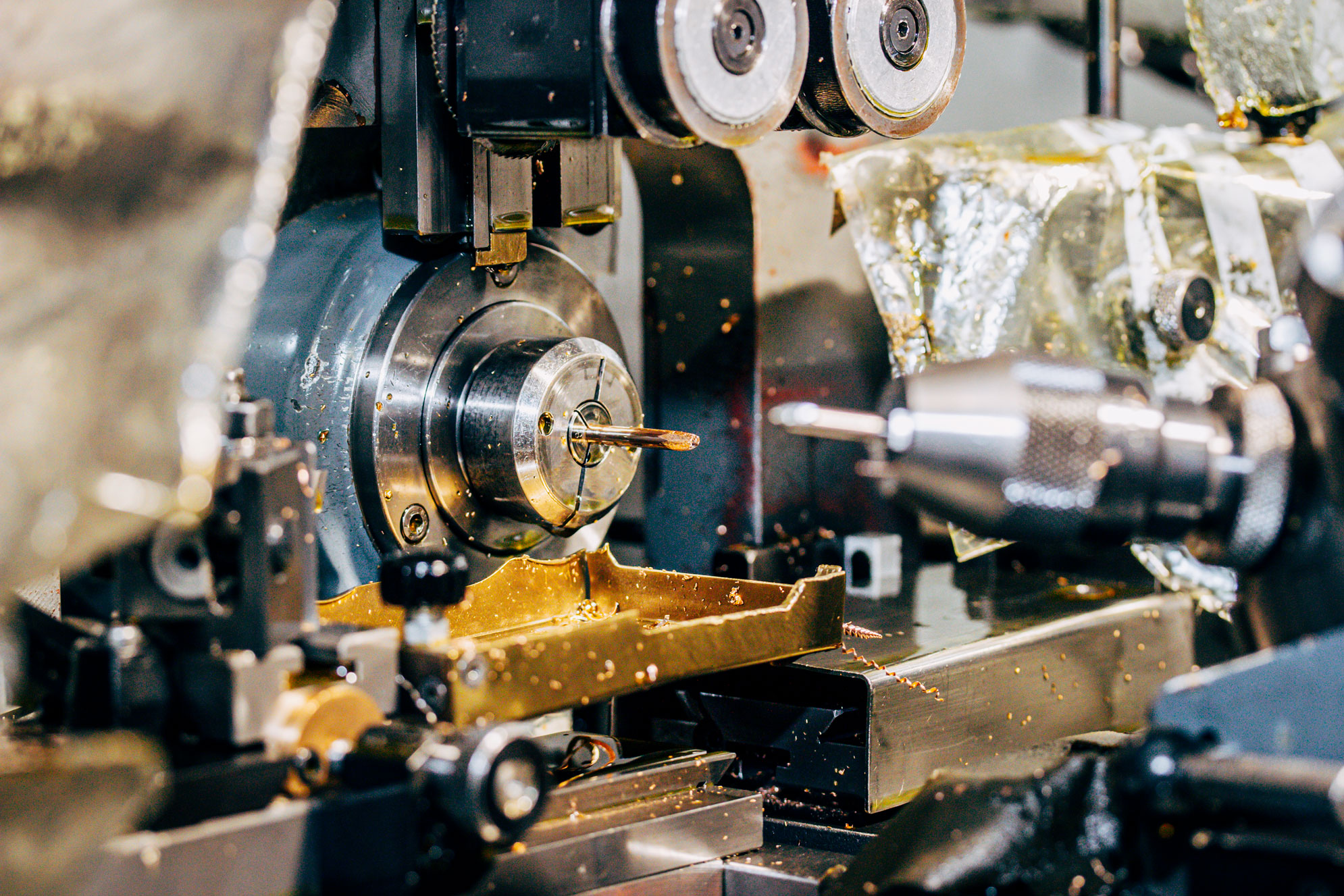
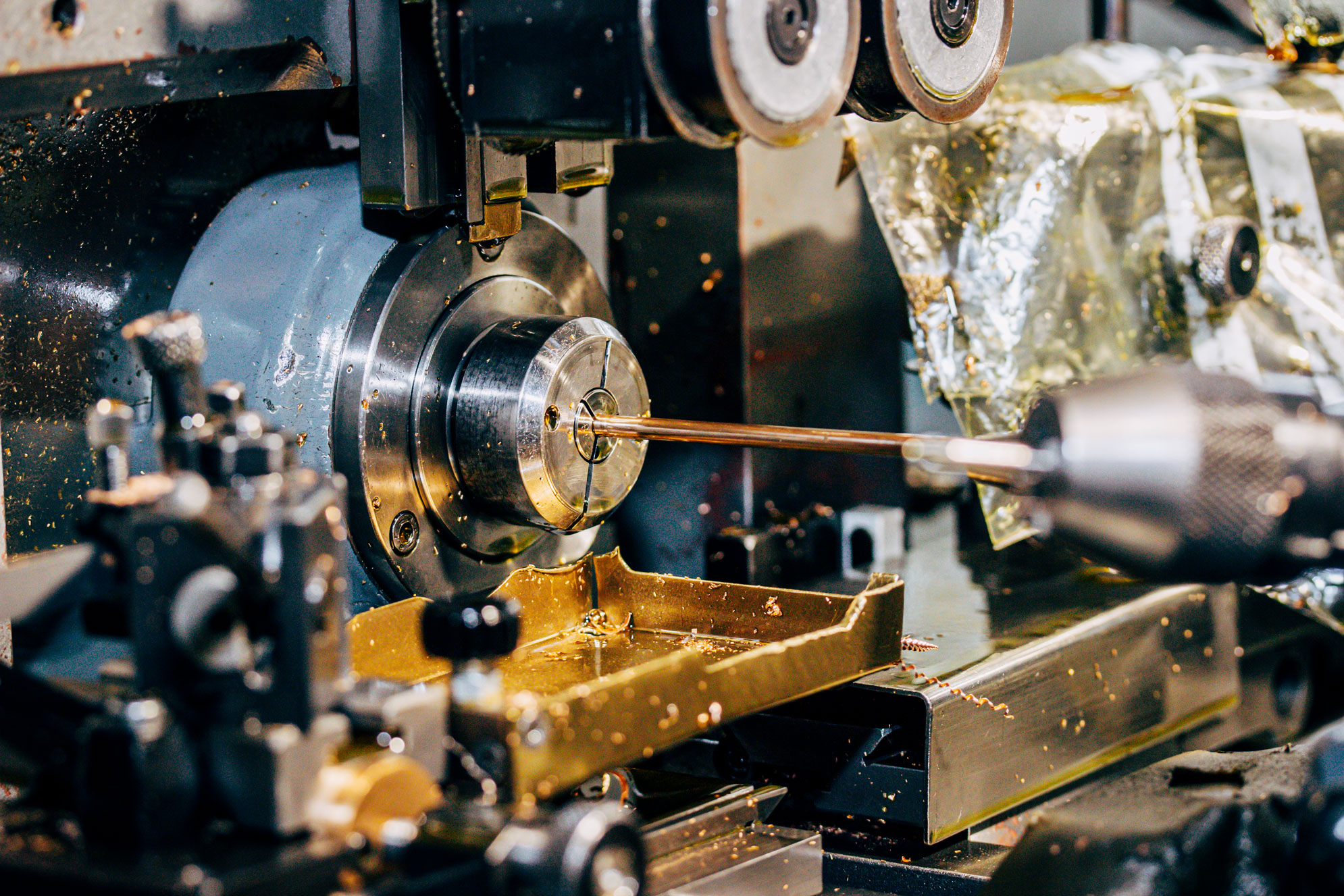
Drilling is the creation of holes inside the material, while the tapping involves the insertion of grooves and details close to the hole previously created. Next, the milling files and defines the shape that the semi-finished product will have in its final processing status, going and removing blunt parts both in the external and internal part.
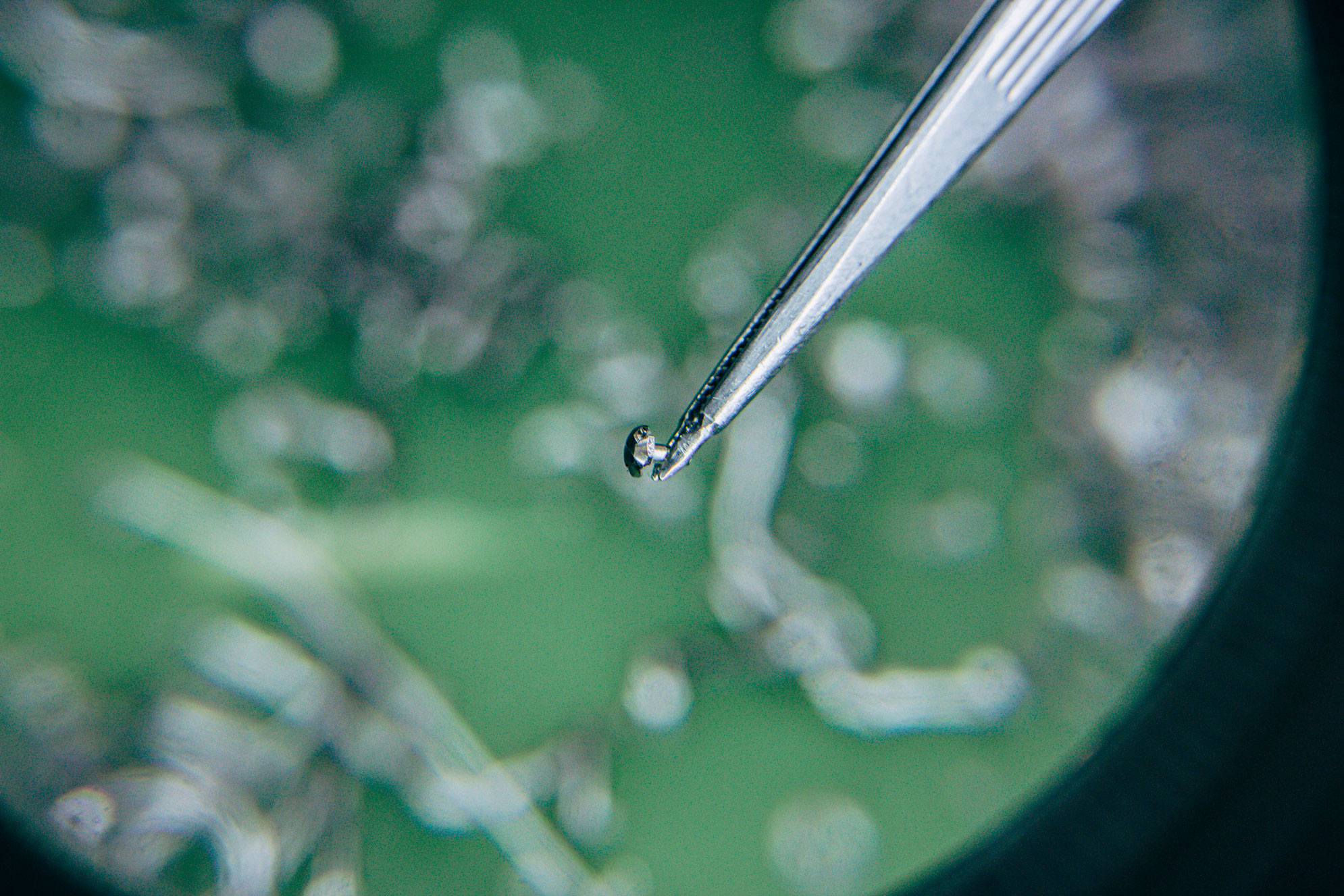
The small metal parts is the starting point of all our works.
Each piece has different sizes and colors depending on the material used: normally, they have a maximum diameter of the components that does not exceed 14 mm. Infact, most of the parts we make measure between 2 and 5 mm in diameter.
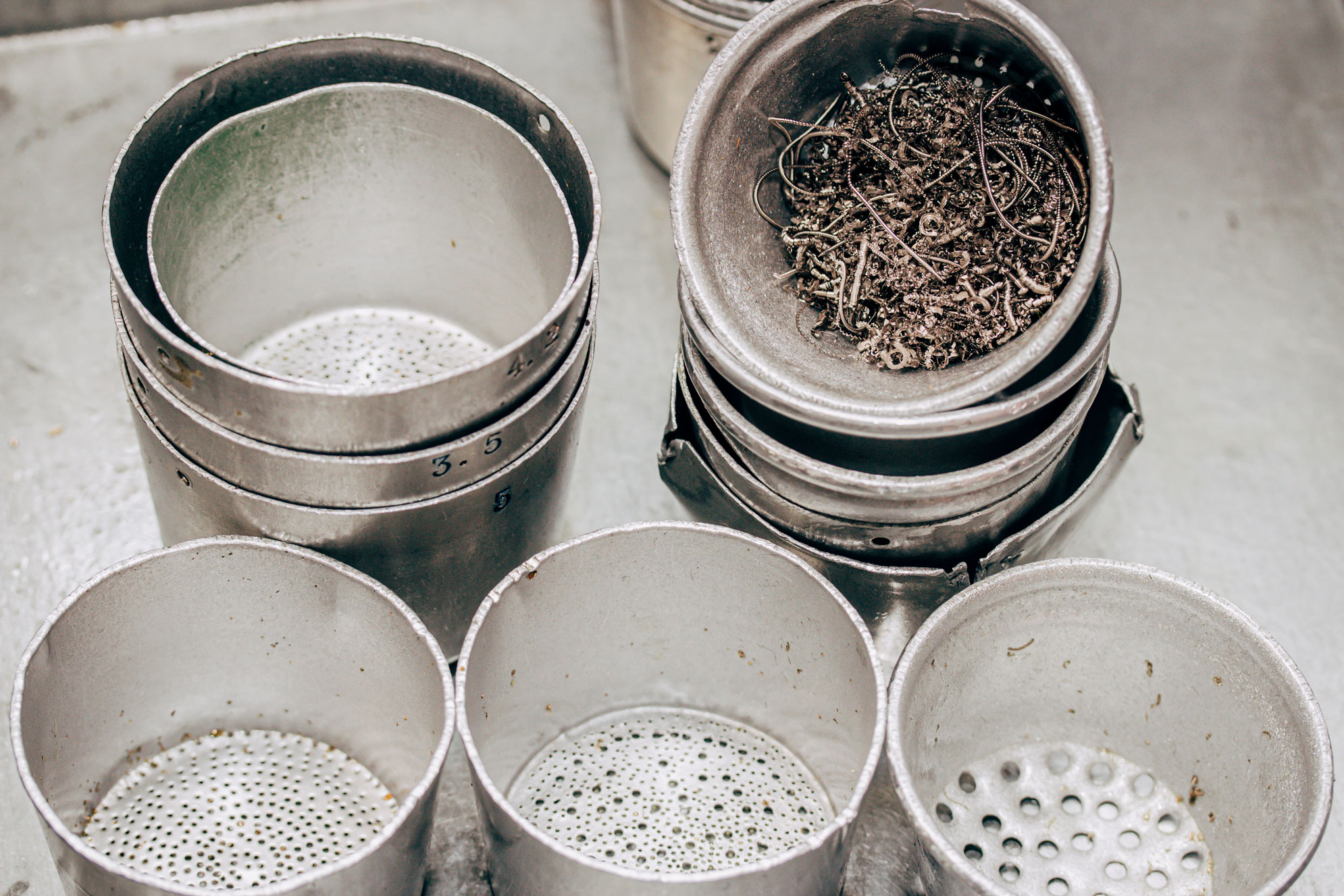
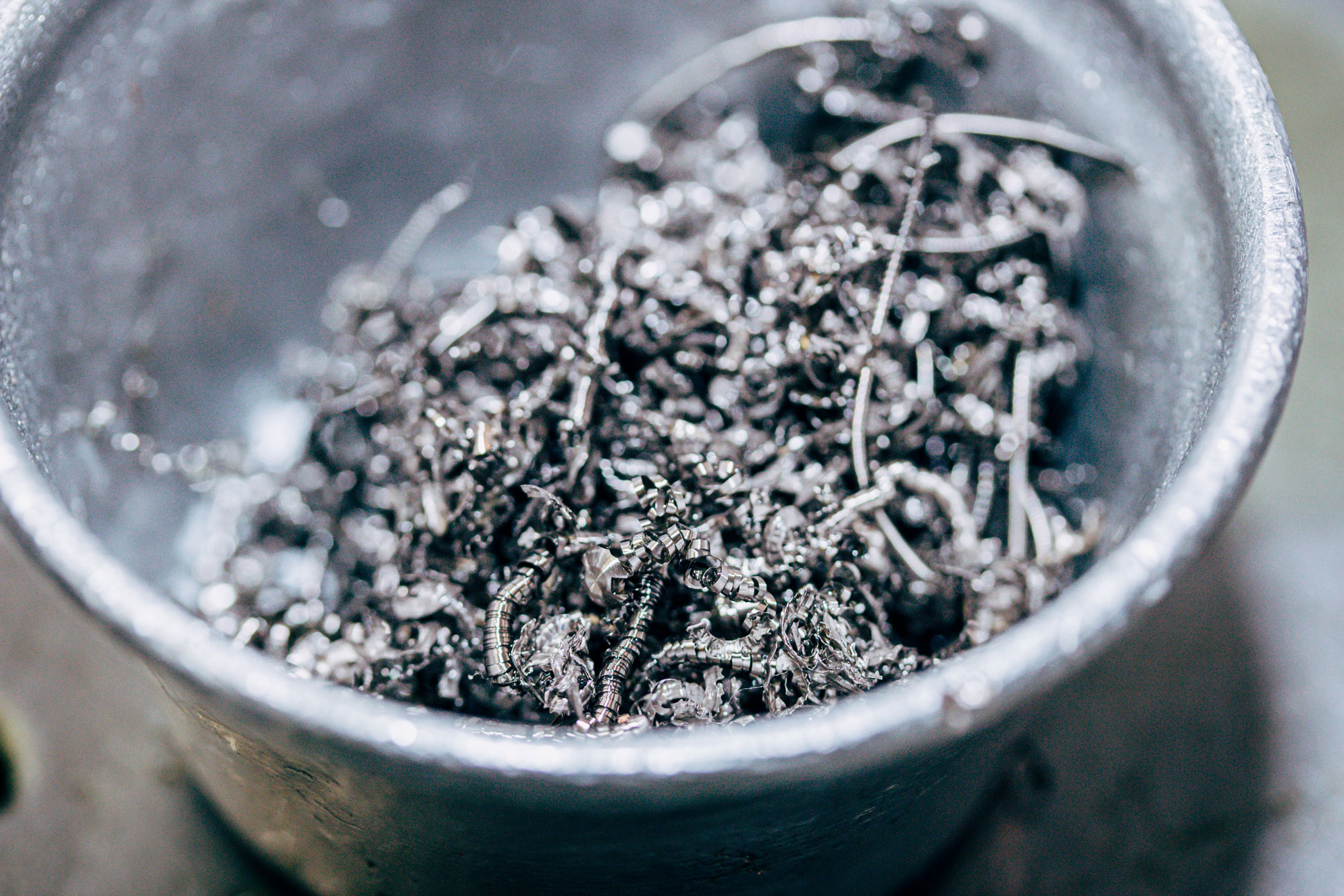
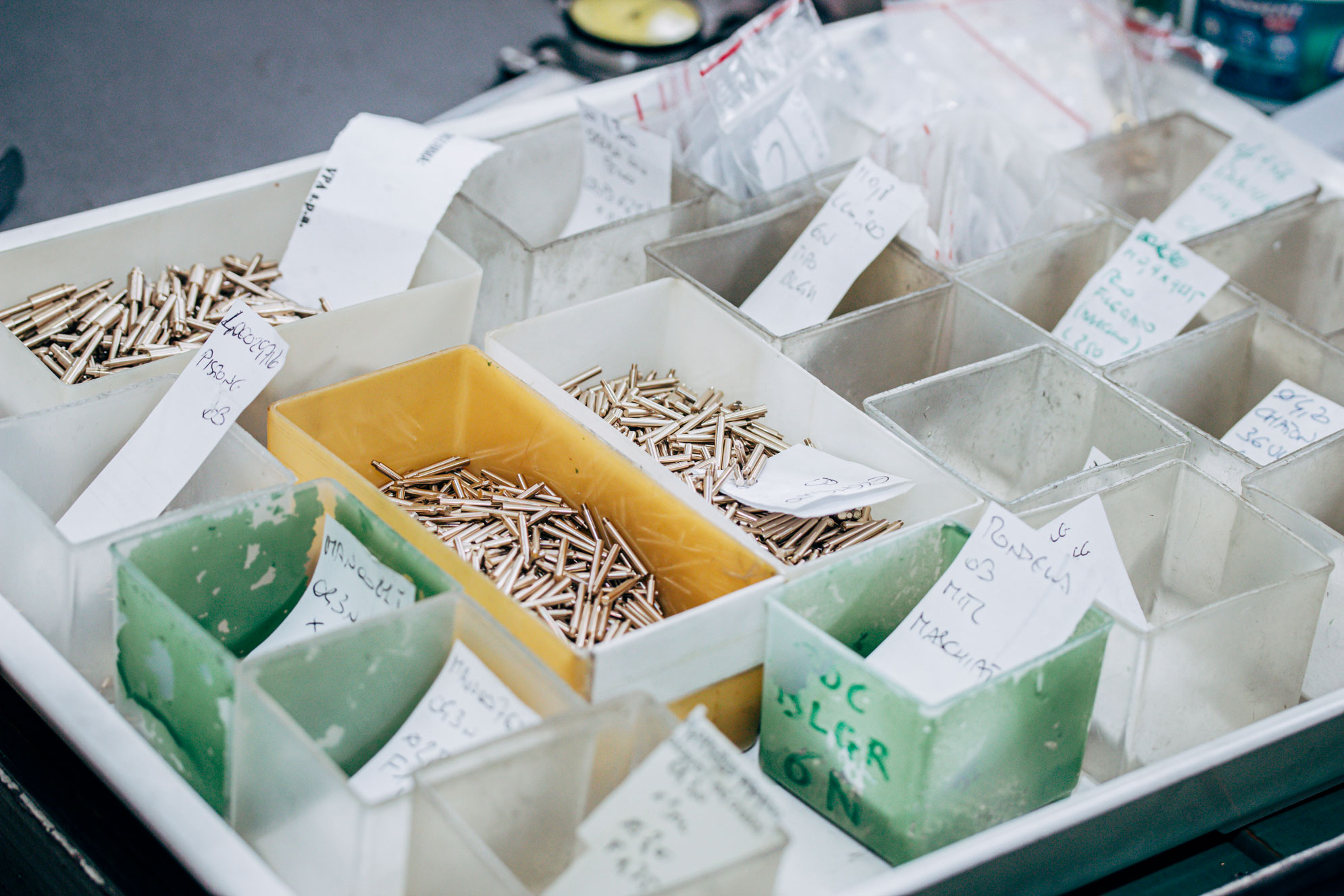
CLEANING
At this stage, the pieces are washed and cleaned: the first process is essential for the selection of small parts while the final cleaning takes place at the end of the production cycle, with the use of specific solvents that eliminate traces of oil and other residues.
Also in the cleaning phase, some smooth models are “tumbled”, polished with the tumbling process – in order to bring out the maximum lucidity of the product.
At the end of this part, the items will be ready, extracted from the basket and delivered to the customer.
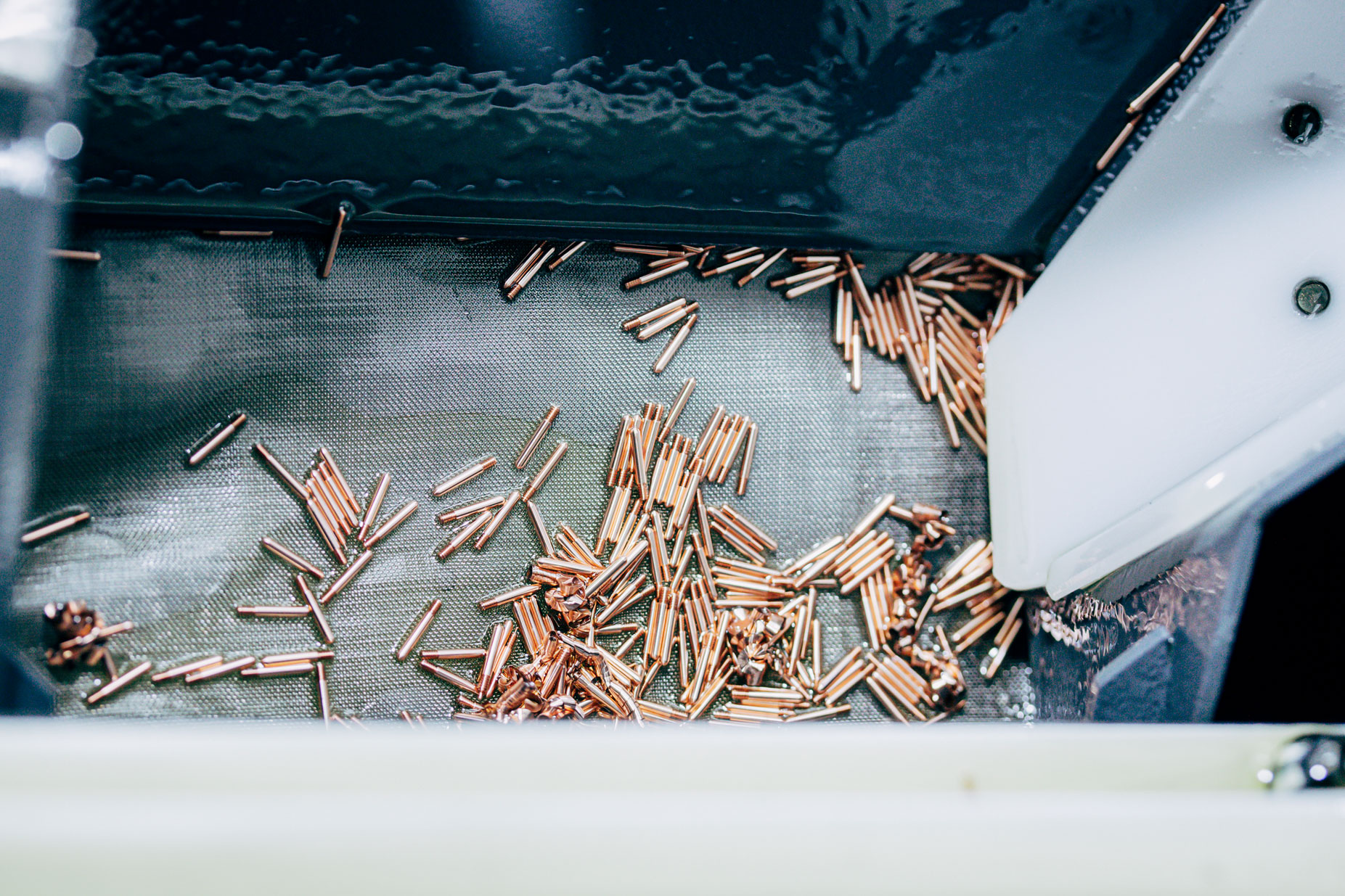